REDEFINING SPLASH ZONE REPAIR
- DIVER-LESS INSTALLATION
- COST EFFECTIVE
- ONLINE INSTALLATION
- INNOVATIVE & TECHNOLOGY ADVANCED
Case Study
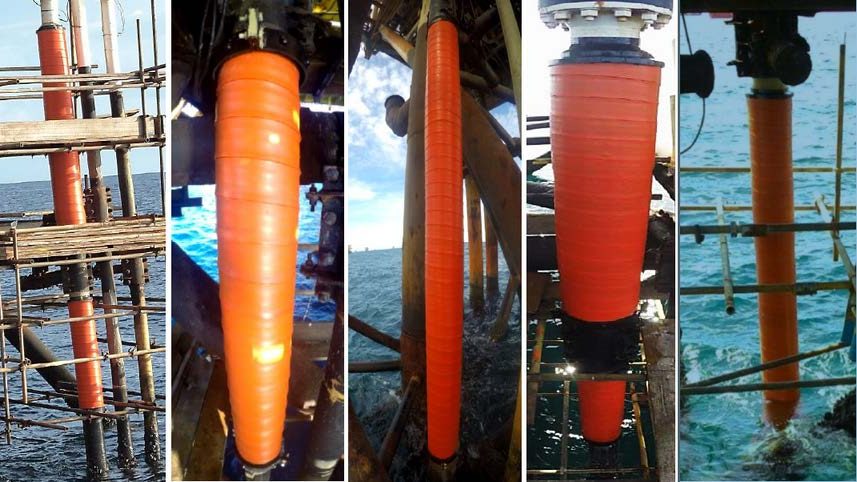
Helicoid Epoxy Sleeve installation was completed successfully, addressing a wall thinning defect at mean sea level on several numbers of riser sizing 6-inches, 8-inches, and 12-inches. The project was professionally executed using a well-defined methodology, involving the surface preparation, installation of the Helicoid Epoxy Sleeve, epoxy
grouting, and curing of the epoxy grout. The Helicoid Epoxy Sleeve was installed successfully, and the riser’s structural integrity was restored without requiring the riser to be shut down.
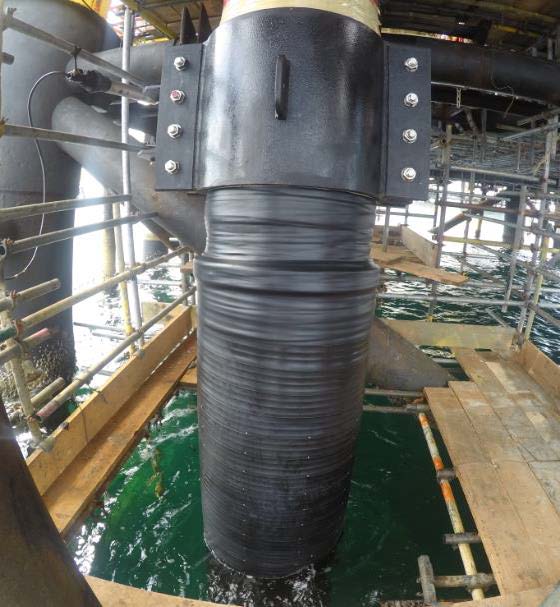
Helicoid Epoxy Sleeve was installed successfully on a 28-inches riser, which addressed a wall-thinning problem at mean sea level. A well-defined procedure was applied to properly carry out the job, which included surface preparation, installation of the Helicoid Epoxy Sleeve, epoxy grouting, and epoxy grout curing. Without having to shut down the riser, the structural integrity of the riser was restored thanks to the successful installation of the Helicoid Epoxy Sleeve.
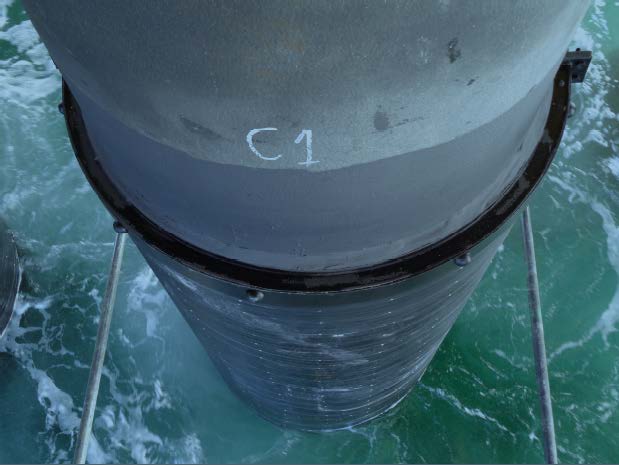
The Helicoid Epoxy Sleeve repair for leaked 40-inch caisson was successfully completed on schedule, addressing a pin hole leak on a 40-
inch caisson at mean sea level. The project was professionally executed using a well-defined methodology, involving the surface preparation, leak containment, installation of the Helicoid Epoxy Sleeve, epoxy grouting, and epoxy grout curing. The Helicoid Epoxy Sleeve was installed successfully, stopping the leak and strengthening the caisson’s structural integrity without requiring the caisson to be shut down. Overall, the project was a success, achieving its desired objectives and minimizing disruption to operations.
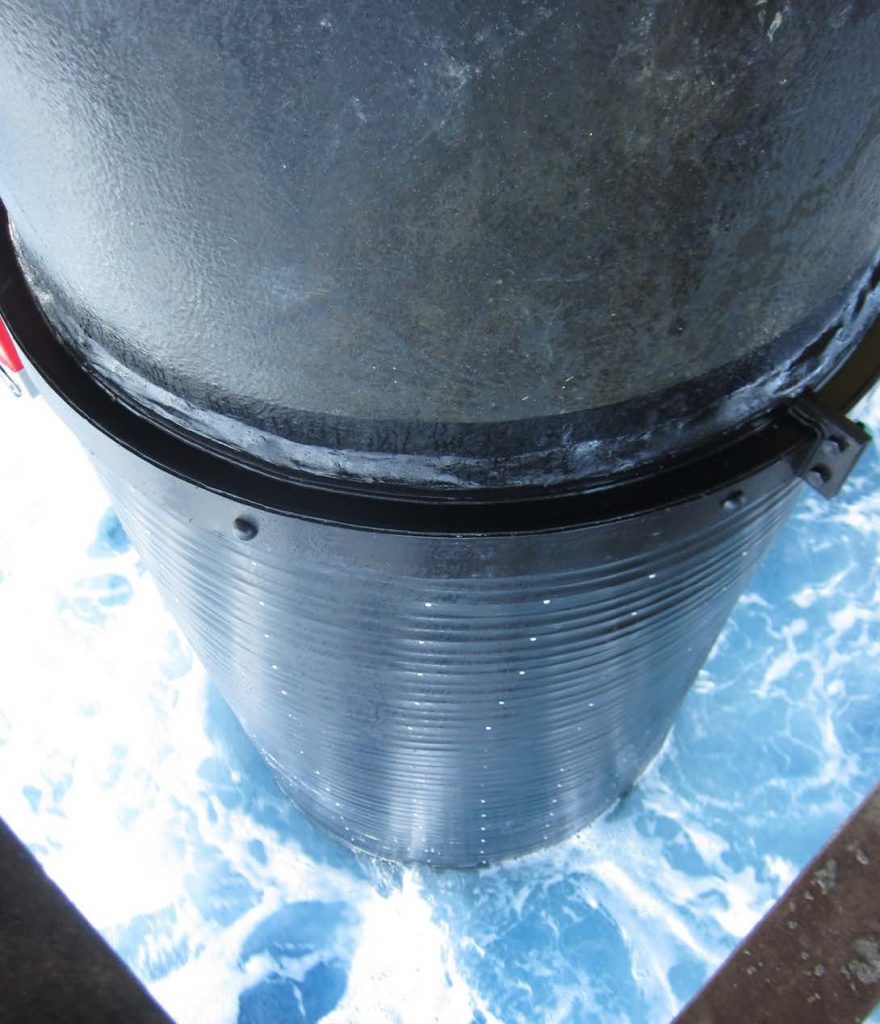
The Helicoid Epoxy Sleeve repair for a leaking 40-inch caisson was completed on time, resolving a pin hole leak on a 40-inch caisson at mean sea level. Surface preparation, leak containment, installation of the Helicoid Epoxy Sleeve, epoxy grouting, and epoxy grout curing were all properly
completed utilizing a well-defined procedure. The Helicoid Epoxy Sleeve was successfully installed, halting the leak and increasing the structural
integrity of the caisson without needing the caisson to be shut down. Overall, the project was a success, meeting its goals while causing minimal disruption to operations.
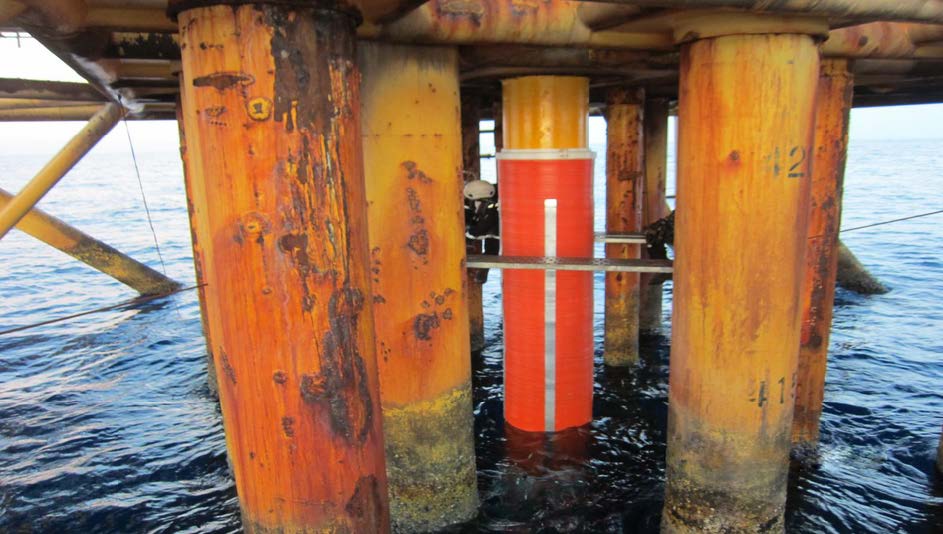
The Helicoid Epoxy Sleeve was successfully installed on a 26-inch conductor, addressing a problem with coating deterioration and wall thinning at mean sea level. The project was completed successfully by following a well-defined protocol that involved surface preparation, installation of the Helicoid Epoxy Sleeve, epoxy grouting, and epoxy grout curing. The successful installation of the Helicoid Epoxy Sleeve allowed the structural integrity of the conductor to be restored without the need to shut down the production.
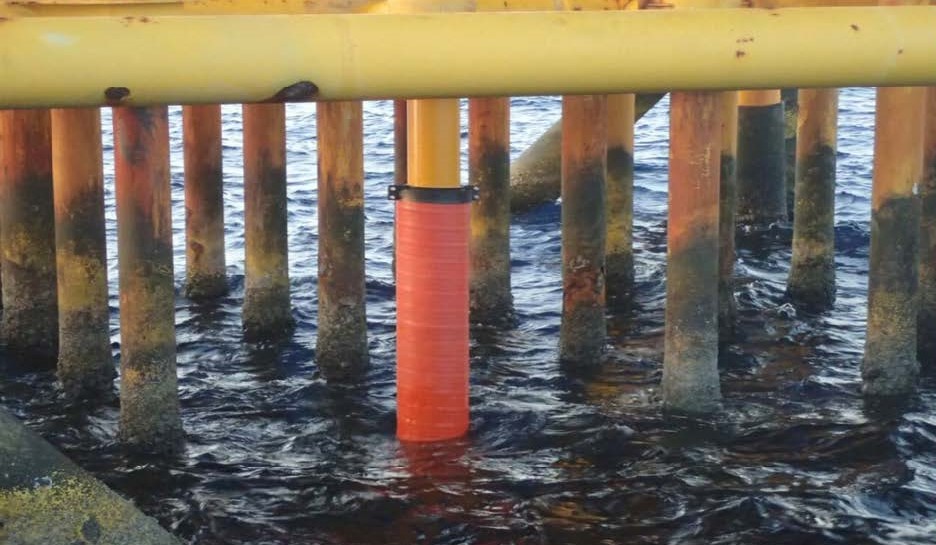
The Helicoid Epoxy Sleeve was successfully installed on a 9-inch conductor to remedy a wall thinning issue at mean sea level. Following a well laid out methodology that included surface preparation, installation of the Helicoid Epoxy Sleeve, epoxy grouting, and epoxy grout curing, the job was successfully completed. The structural integrity of the conductor could have been restored without having to stop production thanks to the successful installation of the Helicoid Epoxy Sleeve.
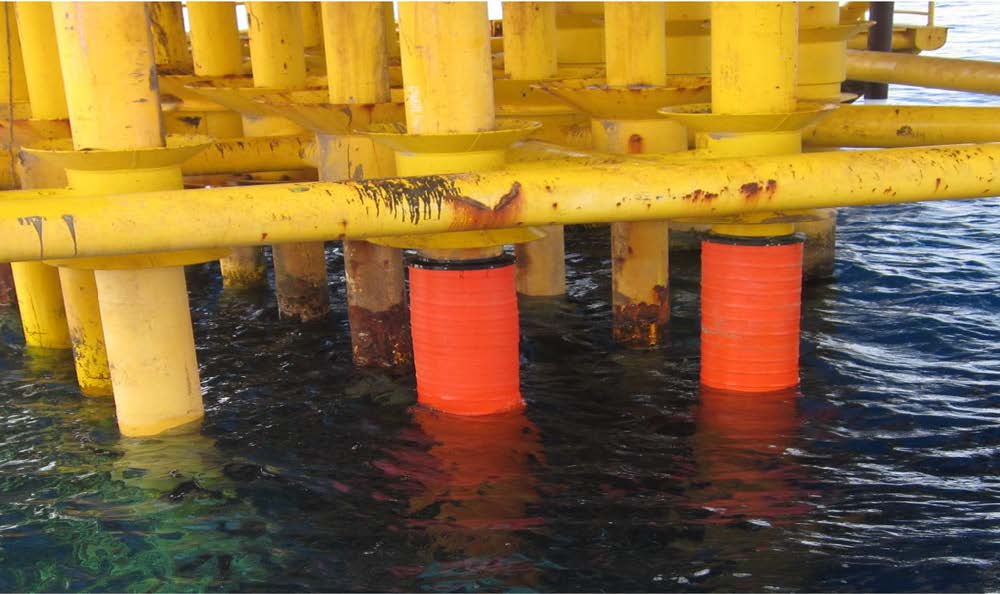
In order to address a wall thinning issue, Helicoid Epoxy Sleeve was successfully fitted on a 12-inch conductor at mean sea level. After following
a well laid out procedure that included surface preparation, installation of the Helicoid Epoxy Sleeve, epoxy grouting, and epoxy grout curing, the job was completed successfully. The structural integrity of the conductor could be restored without having to stop production thanks to the successful installation of the Helicoid Epoxy Sleeve. This is the first ever Helicoid Epoxy Sleeve to be installed.
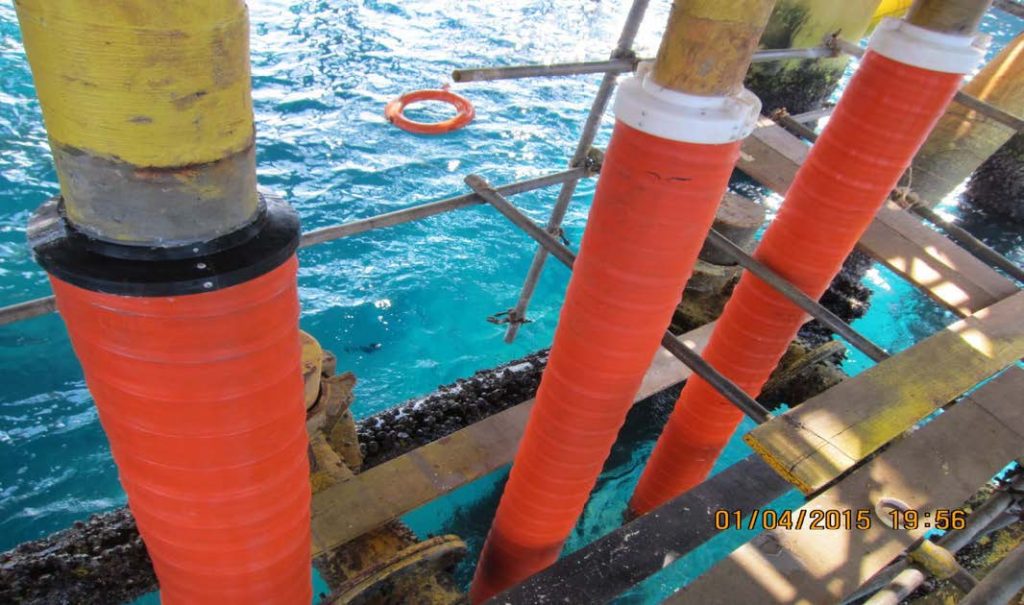
The Helicoid Epoxy Sleeve was successfully put on 6-inch and 8-inch conductors, solving the issue of coating degradation and wall thinning at mean sea level. Following a well laid out methodology that included surface preparation, installation of the Helicoid Epoxy Sleeve, epoxy grouting, and epoxy grout drying, the job was successfully completed. The structural integrity of the conductor has been restored without having to
stop production thanks to the successful installation of the Helicoid Epoxy Sleeve.
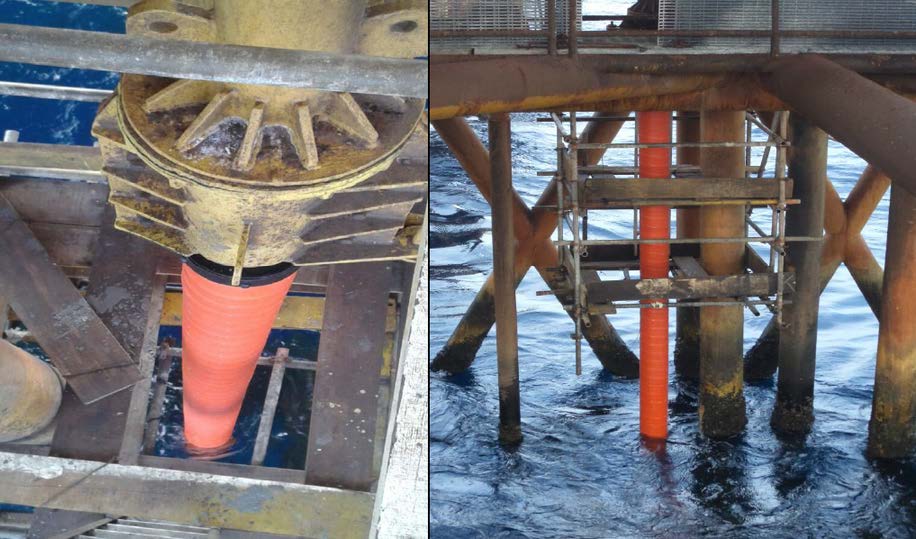
The Helicoid Epoxy Sleeve was successfully installed on a 6-inch conductor, resolving the problem of Neoprene coating deterioration at mean sea level. The task was successfully accomplished after adhering to a well thought out approach that includes surface preparation, installation of the Helicoid Epoxy Sleeve, epoxy grouting, and epoxy grout curing. Thanks to the effective installation of the Helicoid Epoxy Sleeve, the structural integrity of the conductor has been restored without the need to halt production.
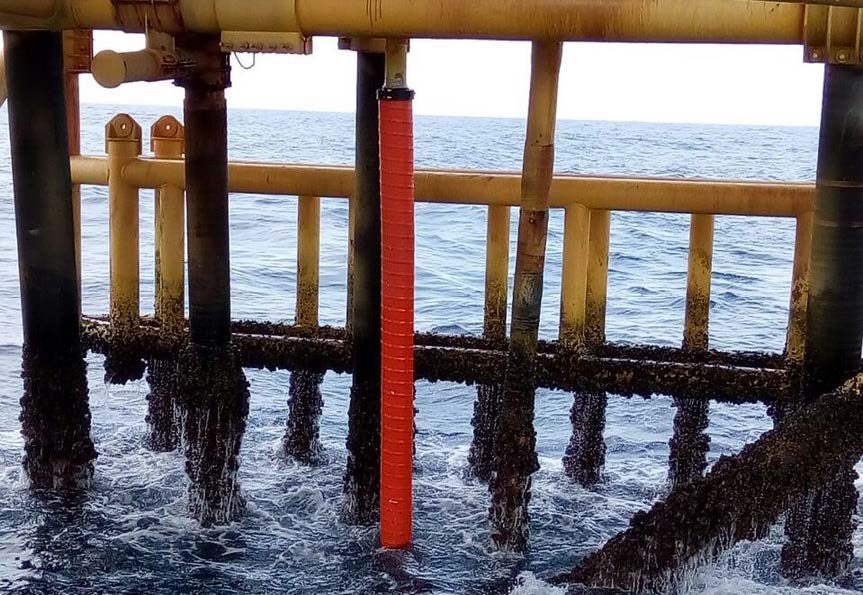
The Helicoid Epoxy Sleeve was successfully fitted on a 6-inch conductor to address the issue of Neoprene coating degradation at mean sea level.
Following a well-considered strategy that involves surface preparation, installation of the Helicoid Epoxy Sleeve, epoxy grouting, and epoxy grout
drying, the work was successfully completed. Without having to stop production, the structural integrity of the conductor has been restored
thanks to the successful installation of the Helicoid Epoxy Sleeve.